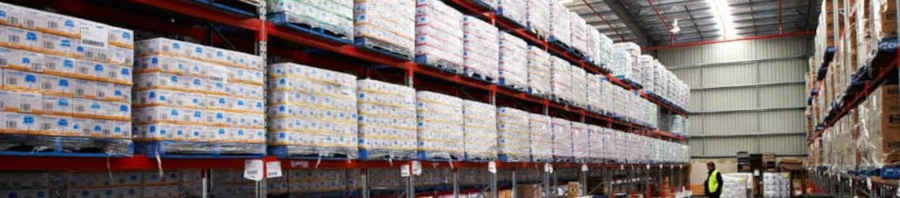
With so many options for warehouse storage, it can be difficult to know which type of pallet racking is best for your space and inventory. In this article, we have listed some of the key areas for your consideration and some questions you should answer about your organisation. We have also created a quick guide to the types of warehouse racking you can view here.
Know What You Are Storing
Knowing what you are storing is a key element to choosing the right racking system. Some systems are designed to take 5000kg per level but others may only have the capability to take 500kg per level. That’s why you should have a general idea of how much your pallets weigh and how much weight the shelves in your new system will need to hold before you choose a racking system
Install A System That Works For YOUR Warehouse
While it may seem simple to just buy an “off-the-shelf” row of racking, a DIY approach can cost you a fortune in underutilised commercial space or the real kicker; a poor workflow that costs thousands of man-hours. No two businesses are alike, and your warehouse operations are unique to your business. Installing a configuration that worked for another company may not work for yours. We offer our years of warehousing experience in a free layout design service to help maximise efficiencies and solve bottlenecks.
Choose A Reputable Australian Company and Australian Made Racks
We all buy cheap international things off eBay and Amazon knowing full well that it’s going to break quicker than something from a reputable brand. But we take the risk to reduce costs and serve the immediate need, hoping that it lasts longer than we expect. However, this isn’t an approach that you should take with warehouse racking. A lot of the products that have been shipped in cheap from overseas are poorly made with cheap steel and they rust.
You also risk your warehouse racking not meeting Australian standards and failing your annual Steel Racking Audit under the racking standards AS4084-2023. Do you have to comply with the racking standards AS4084:2023? If you bought your racking in or after 2012 then the answer is YES.
While the cheap price tag might be appealing, it will cost you when your system breaks down or you have to replace it.
Don’t Risk Second-Hand Racking
Buying second hand can be an easy way to save a couple of bucks. However, when it comes to buying racking, it’s like buying a used car without the service history. You just don’t know what you are getting. Unless you are a racking specialist it’s a toss of the dice gamble.
Some things that need to be factored in when pricing second-hand racking include:
- The racks may not comply with the Australian Standards AS4084:2023
- The system may have been overloaded previously, compromising its integrity
- There may be damage from forklift use or a collision
- The racking company that produced it might not exist any more, limiting your ability to source parts
- You will have to get it certified
- You will have to organise freight
- You will have to pay for installation
Last In First Out or First In First Out
Knowing which of these work best for you will instantly narrow down some of the racking types required.
In a First In First Out racking system the first pallet placed in will be the first pallet out. A simple FIFO racking system is selective racking and a more complex example is pallet flow racking, which is also a high-density solution.
In a Last In First Out racking system, the first pallet placed in will be the last pallet out. A simple LIFO racking system is double deep racking and a more complex example is push back racking.
Take Advantage of Air Space
Do you have a lot of unused air space? Why not install a raised storage area or multi-tier racking system in your warehouse? Installing a raised storage area on top of your racking system can create an additional workspace, a picking area or storage for other large items.
Forklift Accessibility and Aisle Width
When you have a lot of heavy items to move on and off racking you are likely using a forklift. The amount of aisle space required in your racking system must be determined by the type of forklift you have and the truck type.
Increased Storage Capacity
If you’re looking for a pallet racking system that will maximise the storage capacity of your warehouse, a high-density storage system is usually the way to go. These systems are designed for warehouses that store large volumes in individual product lines and typically range from two to ten pallets deep. They are particularly useful for warehouses with a cold room or freezer storage where space may be limited and costly. There are a number of high-density storage systems available which are designed to maximise storage and increase warehouse productivity, including drive-in racking and pallet flow racking.
Questions To Answer About Your Business
Look at your business model
What are our growth forecasts?
What are our plans for expansion?
Are we allowing enough space for adaption?
Look at your industry
What industry factors may change the way our business operates?
Does our industry have seasonal fluctuations?
Are we in a fast-growth industry?
Are we in a fast-moving industry?
Consider how your warehouse moves
What kind of orders do we receive?
Do our products have a limited shelf life?
Do we stock a wide range of items?
Do we stock a lot of a few item types?
Do we have any existing issues?
Do we have any wasted man-hours due to bottlenecks?
Could a new type of racking system solve our problems and save time and money?
Material Handling Equipment
Are we happy with our existing equipment?
Could any of our problems be solved with better racking selection and material handling equipment?